Unlocking Business Growth through Premium Plastic Injection Mold Parts in Metal Fabrication
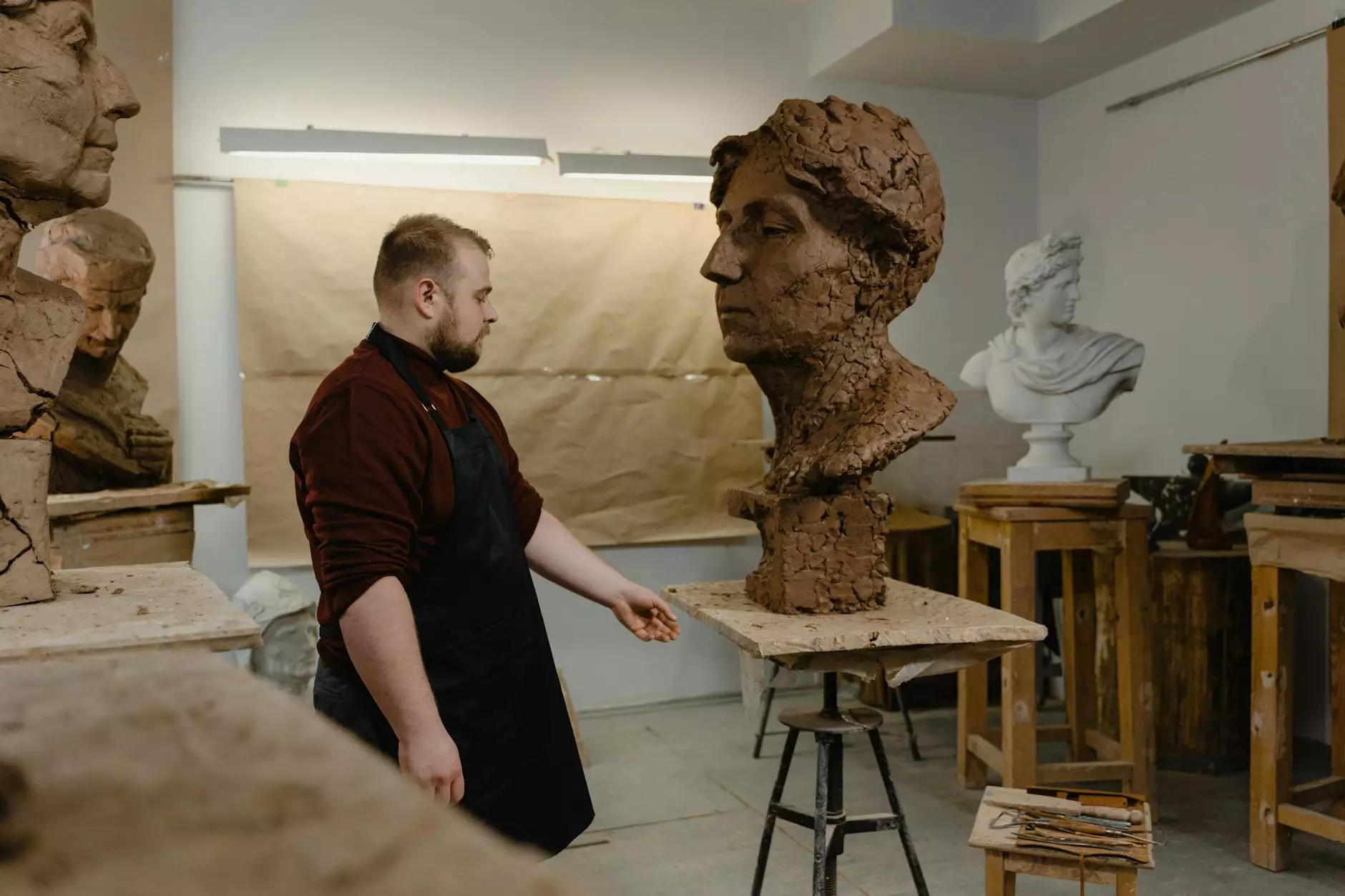
In the highly competitive world of manufacturing, especially within the domain of metal fabricators, the significance of plastic injection mold parts cannot be overstated. These components are the backbone of many complex production processes, offering precision, durability, and versatility that empower businesses to meet the ever-increasing demands of the market.
Understanding the Critical Role of Plastic Injection Mold Parts in Metal Fabrication
Plastic injection mold parts are specialized components used to create precise plastic parts through the injection molding process. When integrated within metal fabrication workflows, they enable the development of prototype components, complex assembly parts, and customized manufacturing solutions. Their role extends far beyond simple molding, influencing the overall quality, efficiency, and innovation potential of a manufacturing enterprise.
Why High-Quality Plastic Injection Mold Parts Are Essential for Business Growth
Utilizing top-tier plastic injection mold parts translates into tangible business benefits, including:
- Enhanced Product Precision: High-quality molds ensure consistency and accuracy in production, reducing waste and rework costs.
- Increased Production Efficiency: Durable and well-designed plastic injection mold parts withstand extensive cycles, facilitating higher output with less downtime.
- Cost Savings: Investing in premium molds minimizes defects and prolongs equipment lifespan, leading to lower operational costs.
- Innovation Capability: Advanced mold technology allows the creation of complex geometries that can distinguish your products in the marketplace.
The Manufacturing Process of Plastic Injection Mold Parts: From Design to Deployment
The journey of plastic injection mold parts from concept to realization is meticulous and requires a comprehensive understanding of materials, design principles, and manufacturing techniques. Here is an in-depth look at each stage:
1. Design and Engineering
Successful molds start with precise design. Engineers utilize CAD/CAM software to create detailed models that consider manufacturing tolerances, material flow, cooling channels, and ejector mechanisms. Innovative designs optimize mold lifespan while ensuring the production of high-quality plastic parts.
2. Material Selection
The choice of materials—such as hardened steel, aluminum, or pre-hardened alloys—directly affects durability, heat resistance, and mold performance. Advanced materials enhance the lifespan of plastic injection mold parts under demanding production conditions.
3. Manufacturing and Fabrication
Modern fabrication techniques, including CNC machining, electrical discharge machining (EDM), and rapid prototyping, enable the creation of highly precise plastic injection mold parts. Quality control during this phase ensures that each part meets strict dimensional and surface finish standards.
4. Assembly and Testing
Assembled molds undergo rigorous testing to verify their integrity and functionality. Simulation software helps predict injection behavior and identify potential issues before full-scale production begins, reducing costs and downtime.
5. Deployment and Maintenance
Once tested, the molds are deployed into production. Regular maintenance, including cleaning and timely repairs, extends the life of plastic injection mold parts, maintaining optimal performance over thousands of cycles.
Innovations in Plastic Injection Mold Parts for Metal Fabricators
The field of plastic injection mold parts is continuously evolving with technological advances, leading to better performance, sustainability, and customization options. Some notable innovations include:
- Multi-Cavity Mold Designs: Increasing productivity by manufacturing multiple identical parts simultaneously.
- Gas-Assist Injection Molding: Reducing material usage and cycle times, resulting in lighter and more cost-effective parts.
- High-Performance Materials: Using thermally conductive or wear-resistant plastics to extend mold life and improve product quality.
- Smart Molds with sensors: Integrating IoT technology for real-time monitoring, predictive maintenance, and process optimization.
Selecting the Right Plastic Injection Mold Parts Supplier
Partnering with a reputable and experienced supplier is crucial to harness the full potential of plastic injection mold parts. Consider the following factors when choosing a supplier:
- Expertise and Experience: Opt for suppliers with a proven track record in metal fabrication and custom mold manufacturing.
- Material Diversity: A wide range of material options ensures the right fit for your specific application.
- Technology and Equipment: Advanced machinery and design capabilities lead to higher precision and better quality.
- Quality Assurance: Certifications like ISO 9001 reflect commitment to consistent quality standards.
- Customer Support: Responsive service and technical consulting help streamline project development.
Deepmould.net: Your Premier Partner in Plastic Injection Mold Parts and Metal Fabrication
At deepmould.net, we specialize in providing top-grade plastic injection mold parts designed specifically for metal fabricators. Our expertise encompasses advanced manufacturing techniques, high-quality materials, and innovative mold designs that meet the most demanding industry standards.
Why choose Deep Mould?
- Customized Solutions: We tailor every plastic injection mold part to your specific needs, ensuring optimal performance and longevity.
- State-of-the-Art Manufacturing: Equipped with cutting-edge machinery for precise, efficient, and scalable production.
- Rigorous Quality Control: Our quality assurance processes guarantee defect-free products that comply with international standards.
- Competitive Pricing and Fast Turnaround: We balance quality with cost-effectiveness and timely delivery.
- Comprehensive Support: Our team provides ongoing technical support and consultation for continuous improvement and innovation.
Maximizing Business Potential with Effective Use of Plastic Injection Mold Parts
Leveraging plastic injection mold parts can significantly transform your manufacturing process, offering opportunities for:
- Product Diversification: Creating complex shapes and integrated assemblies that differentiate your product line.
- Speed to Market: Reducing tooling and production times to respond swiftly to market trends and customer demands.
- Cost Efficiency: Lowering per-unit costs through high-volume production capabilities with durable molds.
- Sustainable Manufacturing: Minimizing waste and energy consumption with precision molds and optimized processes.
- Innovation and R&D: Rapid prototyping with plastic injection mold parts accelerates product development cycles.
Conclusion: Elevate Your Business with Superior Plastic Injection Mold Parts in Metal Fabrication
Plastic injection mold parts play an indispensable role in modern metal fabrication, underpinning quality, efficiency, and innovation. By investing in high-quality molds and forging strategic partnerships with experienced suppliers like deepmould.net, your manufacturing business can achieve remarkable growth, market differentiation, and sustained competitive advantage.
Embrace the future of manufacturing with precision-engineered plastic injection mold parts that meet your evolving needs. Harness their potential to unlock new product capabilities, streamline operations, and grow your business exponentially.