The Comprehensive Guide to Plastic Injection Molds
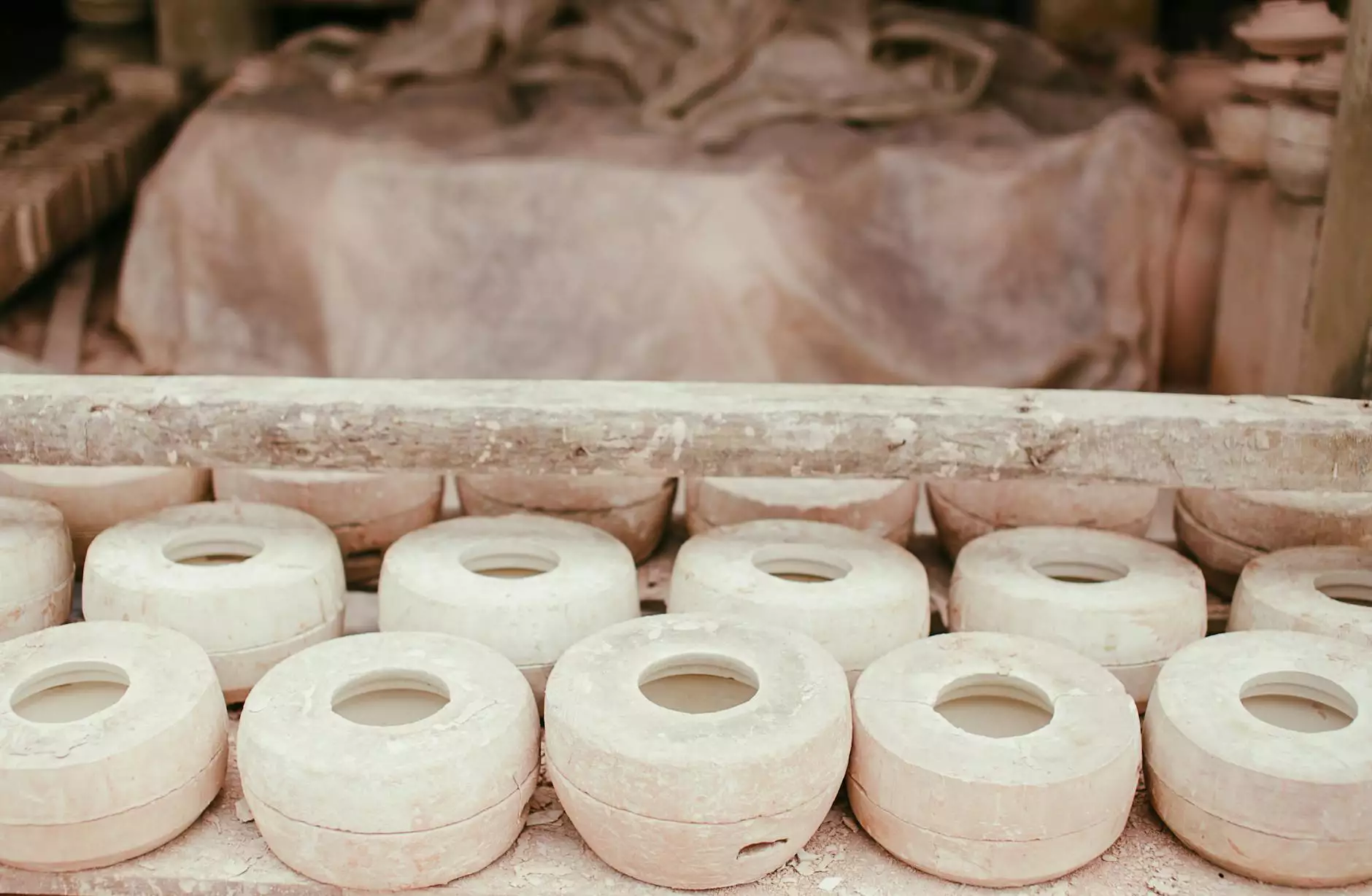
Plastic injection molds are at the heart of modern manufacturing processes across various sectors. Their ability to produce intricate components with precision makes them invaluable in multiple industries, from automotive to consumer goods. This article delves into the intricacies of plastic injection molding, offering insights into the manufacturing process, benefits, applications, and why choosing the right provider, like Deep Mould, is crucial for your business success.
Understanding Plastic Injection Molding
The plastic injection molding process involves the creation of plastic parts by injecting molten plastic into a mold. This technique is renowned for its efficiency and ability to produce high volumes of quality components. Let’s break down the core elements of this process:
The Manufacturing Process
- Designing the Mold: The journey begins with designing a mold that meets the specifications of the intended product. Advanced CAD software is often used to create precise designs.
- Material Selection: Various types of plastic can be used, including thermoplastics and thermosetting plastics. The choice depends on the required properties of the final product.
- Heating the Plastic: The selected plastic materials are heated until they reach a molten state, making them pliable for molding.
- Injection into the Mold: The molten plastic is injected under high pressure into the prepared mold cavity, allowing it to fill every detail of the design.
- Cooling and Solidification: After injection, the plastic is cooled, solidifying within the mold. This step is crucial for ensuring dimensional accuracy.
- Mold Removal: Once solidified, the mold opens, and the finished product is ejected. This cycle then repeats for the next batch.
Advantages of Plastic Injection Molding
Plastic injection molding presents a myriad of advantages that make it the method of choice for many manufacturers:
- High Efficiency: The ability to produce large quantities of parts in a short time frame makes this process extremely efficient.
- Design Flexibility: Complex shapes and intricate designs can be easily achieved, allowing for creative freedom in product development.
- Cost-Effectiveness: Although the initial cost of molds can be high, the low per-unit cost at high volumes often results in significant savings.
- Consistency and Quality: The process ensures that each product is identical, maintaining high standards of quality throughout production.
- Reduced Waste: The precise dosing of materials leads to minimal waste, contributing to a more sustainable manufacturing process.
Applications of Plastic Injection Molds
The applications of plastic injection molds are extensive and span various industries. Here are some primary sectors where they play a crucial role:
Automotive Industry
In the automotive sector, plastic injection molding is used to manufacture components such as dashboards, door panels, and interior trims, among other products. The lightweight nature of plastic helps improve fuel efficiency while still providing durability.
Consumer Goods
Everyday items, from containers to kitchen utensils, are often produced using injection molding. Products can be designed to be lightweight, colorful, and ergonomically friendly.
Electronics
In the electronics field, the process is used to create housings, connectors, and intricate components that require excellent thermal and electrical properties.
Medical Devices
The medical industry relies on injection molded parts for various applications, including surgical instruments, drug delivery systems, and even wearable health technology. Molds used in this field must adhere to strict regulatory standards to ensure safety and effectiveness.
Toys and Sporting Goods
The toy industry benefits greatly from plastic injection molding, where vibrant colors and detailed designs can attract children's interest while ensuring safety through high-quality materials.
Deep Mould: Your Partner in Plastic Injection Molds
At Deep Mould, we understand that the success of your products hinges on the quality of the molds used to create them. Our commitment to excellence is evident in our rigorous standards and innovative manufacturing processes. Here’s why Deep Mould stands out:
Expert Design and Engineering
We employ a team of highly skilled engineers and designers who leverage state-of-the-art technology to create precise and efficient mold designs tailored to your specific needs.
High-Quality Materials
Understanding that the quality of materials directly impacts the performance of molds, we source only the finest raw materials, ensuring longevity and reliability in every product.
State-of-the-Art Manufacturing Processes
Our manufacturing facilities are equipped with the latest machinery and technology, allowing us to produce complex molds with high accuracy in less time.
Comprehensive Support
From the initial design phase through to production, our dedicated support team is there to assist you at every step, ensuring your expectations are not just met, but exceeded.
Commitment to Sustainability
We are committed to environmentally friendly practices, making efforts to reduce waste and promote recycling throughout our manufacturing operations.
Choosing the Right Plastic Injection Mold Supplier
Selecting the right partner for your plastic injection molds is critical for ensuring the quality and performance of your final products. Consider the following factors:
Experience and Specialization
A provider with extensive experience in plastic injection molding will be better equipped to navigate common challenges and meet your specific needs. Look for a supplier that specializes in your industry for tailored solutions.
Innovation and Technology
In the fast-paced world of manufacturing, being at the forefront of technology is essential. Ensure your supplier invests in the latest technology to enhance production efficiency and quality.
Quality Assurance Processes
Ask about the quality control measures in place. A reputable supplier will implement strict quality assurance protocols to ensure that every mold produced meets high standards.
Customer Reviews and Testimonials
Take the time to read reviews and testimonials from previous customers. Their experiences will provide valuable insights into the reliability and performance of the supplier.
The Future of Plastic Injection Molding
As industries evolve, the field of plastic injection molding is also advancing. The future will see more use of advanced materials, automation, and sustainability practices. Here are some trends to watch:
- Advanced Materials: The development of new plastics, including bioplastics, will likely support a push towards more sustainable products.
- Automation: The integration of robotics in the manufacturing process is expected to enhance efficiency and reduce production costs.
- Smart Manufacturing: The use of IoT and smart technologies will optimize manufacturing processes, allowing real-time tracking and quality control.
Conclusion
Plastic injection molds are a cornerstone of successful manufacturing operations, facilitating the production of high-quality, complex components across various industries. Choosing a reliable partner like Deep Mould ensures that your manufacturing needs are met with expertise and high standards. With a commitment to quality, innovation, and customer satisfaction, Deep Mould is poised to help your business achieve its production goals and thrive in a competitive landscape.