Understanding the Role of a Lathe Machine Part Company in Modern Manufacturing
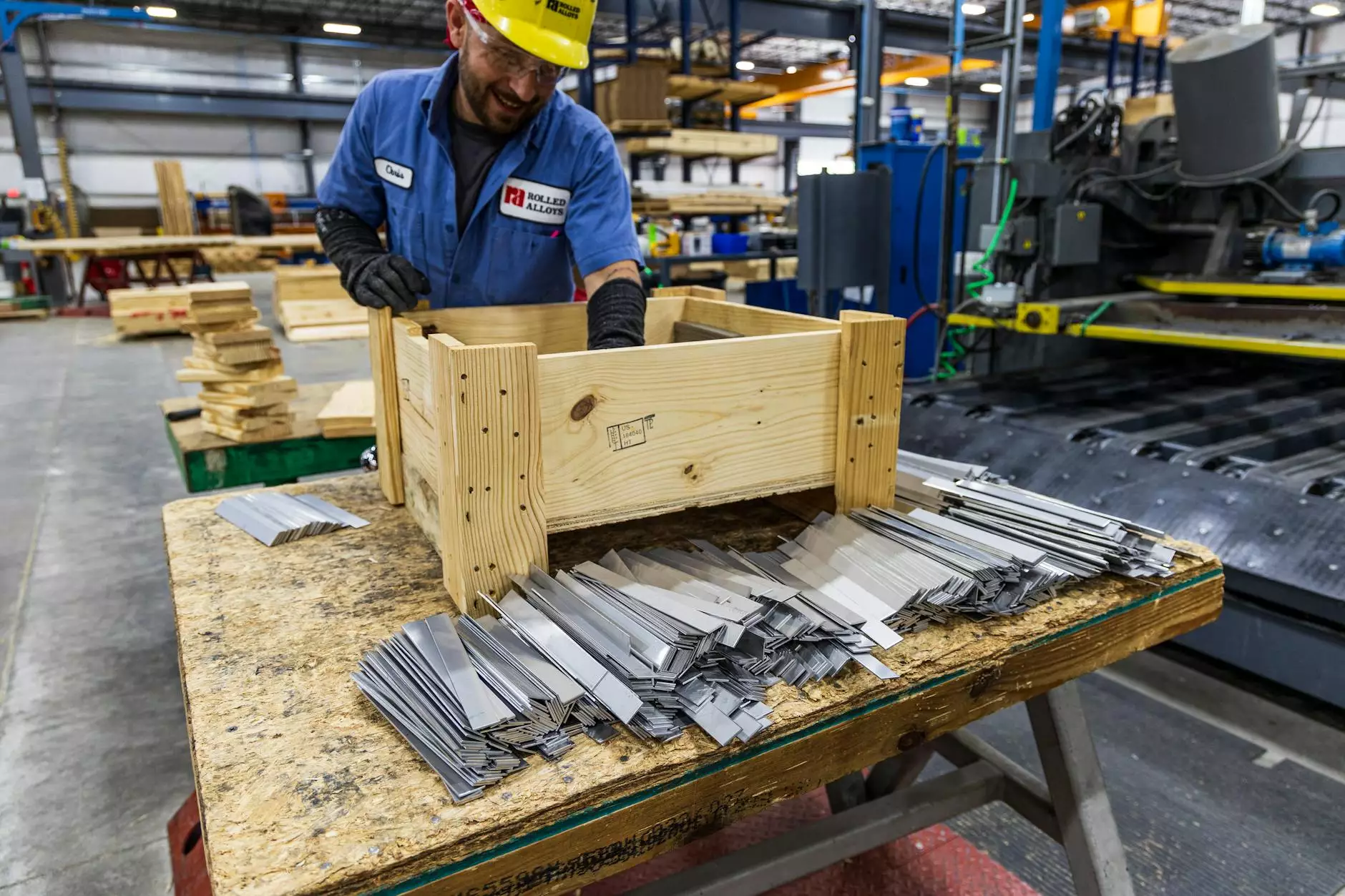
The lathe machine part company plays a pivotal role in the metal fabrication industry, providing essential components that support various manufacturing processes. This article delves into the intricacies of lathe machines, the significance of precision parts, and how organizations like Deep Mould are leading the way in innovation and quality.
What is a Lathe Machine?
A lathe machine is a versatile tool used for shaping and machining materials, primarily metals. The primary function of a lathe is to rotate the workpiece against cutting tools to create precise shapes and dimensions. Key components of lathe machines include:
- Headstock: Houses the main spindle and motor.
- Tailstock: Supports the other end of the workpiece and can hold drills and other accessories.
- Bed: The main structure that holds the headstock, tailstock, and carriage.
- Carriage: Moves the cutting tool over the workpiece.
- Chuck: Holds the workpiece securely in place during operation.
The Importance of Precision Parts in Metal Fabrication
In a world where precision and accuracy are paramount, a lathe machine part company focuses on producing high-quality components that ensure the functionality and reliability of end products. The manufacturing processes that utilize lathe machines, such as:
- Automotive Manufacturing: Producing precise components for engines, transmissions, and chassis.
- Aerospace Engineering: Crafting crucial parts that must meet stringent safety standards.
- Medical Equipment: Creating intricate parts for devices that require high levels of accuracy.
Precision parts not only enhance the performance of machinery but also extend their lifespan, reducing the need for frequent replacements and the associated costs.
The Process of Manufacturing Lathe Machine Parts
The manufacturing of lathe machine parts involves several steps, each critical to ensuring the final product meets industry standards. These steps include:
- Material Selection: Choosing the right materials, such as aluminum, stainless steel, or titanium, based on the required strength and durability.
- CNC Machining: Utilizing Computer Numerical Control (CNC) technology to achieve high precision and repeatability in part production.
- Quality Control: Implementing rigorous testing protocols to ensure each part meets predefined specifications.
- Finishing Touches: Applying processes like polishing, coating, or anodizing to enhance the appearance and performance of the parts.
How a Lathe Machine Part Company Enhances Production Efficiency
Companies like Deep Mould prioritize efficiency in their operations. By investing in state-of-the-art machinery and employing skilled professionals, they ensure that:
- Reduced Lead Times: Streamlined processes allow for quicker turnaround from concept to production.
- Cost-Effectiveness: Efficient production methods minimize waste and reduce overall costs, benefiting clients significantly.
- Custom Solutions: The ability to produce bespoke parts tailored to client specifications leads to greater customer satisfaction.
The Impact of Technology on Lathe Machine Part Manufacturing
Technological advancements have profoundly impacted the metal fabrication industry. Some of the latest trends shaping the future of lathe machine part manufacturing include:
- Automation: Automation reduces human errors and increases production speed.
- 3D Printing: This technology allows for the rapid prototyping of parts, accelerating the design process.
- Internet of Things (IoT): IoT integration facilitates real-time monitoring of machines, enhancing maintenance and reducing downtime.
Quality Assurance in Lathe Machine Part Manufacturing
Quality assurance is a cornerstone of any lathe machine part company. Ensuring that each product meets high standards involves:
- Regular Inspections: Routine checks at various stages of production help identify potential issues early.
- Standards Compliance: Adhering to international standards such as ISO ensures that products meet global quality expectations.
- Feedback Mechanisms: Engaging with clients for feedback allows continuous improvement in product quality.
Choosing the Right Lathe Machine Part Company: What to Look For
Selecting the right lathe machine part company is crucial for any business relying on precision-engineered components. Here are some essential factors to consider:
- Experience: Companies with a proven track record often provide higher quality and reliability.
- Capabilities: Evaluate whether the company has the necessary machinery and technology to meet your specific needs.
- Customer Support: Strong customer service is vital for addressing concerns and ensuring smooth communication.
- Certifications: Look for companies with relevant industry certifications that indicate adherence to quality standards.
The Future of Lathe Machine Parts Manufacturing
The future of manufacturing lathe machine parts is bright. As industries continue to evolve, so do the demands for precision, efficiency, and innovation. Key trends to watch include:
- Increased Customization: As markets become more niche, the demand for customized solutions continues to rise.
- Sustainability: A growing focus on sustainable practices in manufacturing will influence production methods and materials.
- Integration of AI: Artificial Intelligence will further enhance operations by optimizing processes and improving decision-making.
Conclusion
In summary, the lathe machine part company landscape is vital for various manufacturing sectors, offering precision components that drive operational efficiency and product reliability. Companies like Deep Mould are setting high standards through advanced technology, rigorous quality assurance, and exceptional customer service. As we look to the future, staying ahead of industry trends will be key to continued success in this essential field.