Understanding Plastic Injection Molds: The Key to Quality Manufacturing
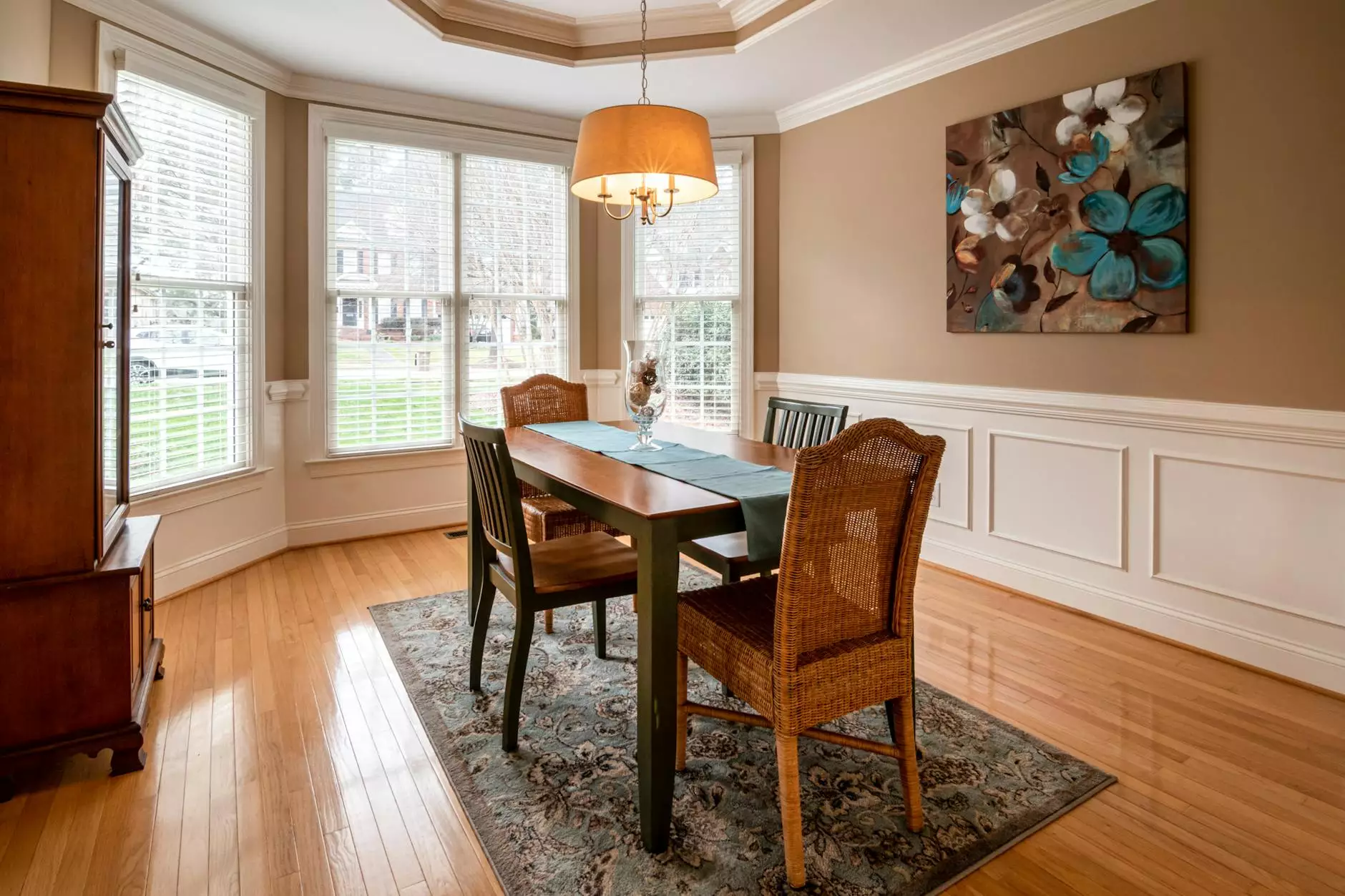
In today's competitive manufacturing landscape, the ability to create high-quality products efficiently is essential for businesses striving to stay ahead. One pivotal technology that facilitates this is plastic injection molding. This method has revolutionized how products are designed and fabricated, making it easier to produce complex geometries with precision. If you're considering the option to buy plastic injection molds, understanding the intricacies and benefits of this process can empower your business decisions.
What are Plastic Injection Molds?
Plastic injection molds are specialized tools used in the injection molding process, wherein molten plastic is injected into a mold cavity to create specific shapes. This process is widely employed across various industries, from consumer goods to automotive and medical devices.
Key Components of Plastic Injection Molds
To comprehend how to effectively buy plastic injection molds, it's crucial to understand their components:
- Cavity: The interior shape of the mold that dictates the object's final geometry.
- Core: The counterpart to the cavity that forms the interior details of the product.
- Injection System: Includes the nozzle and runners that channel molten plastic into the mold.
- Cooling System: Aids in managing the temperature of the mold to solidify the plastic efficiently.
- Ejection System: Mechanism to remove the finished product from the mold without damage.
The Advantages of Using Plastic Injection Molding
Investing in high-quality plastic injection molds offers numerous benefits that can positively impact your business operations:
1. High Efficiency and Speed
Once a mold is designed and constructed, the manufacturing process can be highly automated, leading to faster production cycles. This efficiency allows you to scale your operations without compromising on quality.
2. Precision and Consistency
Plastic injection molding enables the production of complex shapes with high precision. This accuracy ensures that every part manufactured is consistent, which is crucial in industries like automotive and aerospace where quality standards are stringent.
3. Material Versatility
This process works with a wide variety of thermoplastic materials, providing flexibility in product design and function. Whether you require durable components or more flexible parts, injection molding offers suitable material options.
4. Cost-Effectiveness for Large Production Runs
While the initial investment for high-quality molds can be significant, the cost per unit decreases dramatically as production volumes increase. This economy of scale makes it a favorite among manufacturers looking to produce large quantities of items.
5. Eco-Friendly Manufacturing
Modern injection molding processes are increasingly designed to be eco-friendly. They utilize materials efficiently, recycle scrap plastic, and reduce waste, aligning with sustainability goals in today’s manufacturing landscape.
How to Buy Plastic Injection Molds
Acquiring the right plastic injection molds is a strategic investment. Here are the steps to ensure you make a well-informed decision:
1. Define Your Requirements
Before you buy plastic injection molds, outline the specifications based on your production needs. Consider factors such as:
- The type of product you are producing
- Material type
- Production volume
- Budget constraints
2. Research Reputable Suppliers
Look for suppliers with a proven track record in the industry. Reading reviews, seeking recommendations, and visiting their facilities can provide insights into their capabilities and reliability. A great option is Deepmould, known for excellent service in metal fabricators.
3. Assess the Quality of Molds
Quality should be a major focus when choosing molds. Examine materials used, design precision, and life expectancy of the molds. Request samples or case studies from the supplier to evaluate their work quality.
4. Discuss Custom Design Options
If your project demands specific features, inquire about custom mold design services. Experienced manufacturers can provide tailored solutions to meet unique project requirements.
5. Understand the Lead Time
The time frame for mold production can vary significantly. Be sure to discuss and understand delivery timelines upfront to align with your production schedule.
6. Evaluate After-Sales Support and Maintenance
Quality doesn’t stop at the purchase. Ensure your supplier offers solid after-sales support, maintenance services, and guidance for mold repair. This ongoing relationship can significantly extend the life of your investment.
Common Mistakes to Avoid When Buying Plastic Injection Molds
While the journey to buy plastic injection molds can be rewarding, there are common pitfalls that businesses should avoid:
- Insufficient Research: Failing to fully understand the supplier's capabilities can lead to subpar molds and lost production time.
- Underestimating Costs: Always factor in the long-term costs associated with mold maintenance, repairs, and machine operation in your budget.
- Ignoring Design Iterations: The first design may not always be perfect. Be open to revisions and improvements throughout the process.
- Neglecting Training: Ensure that your team is adequately trained to use and maintain the molds to prevent operational problems and downtime.
The Future of Plastic Injection Molding
The plastic injection molding industry continues to evolve, driven by advancements in technology and a growing emphasis on sustainability. Some emerging trends include:
1. Automation and Smart Manufacturing
Incorporating IoT and AI in manufacturing processes can help optimize production efficiency and quality assurance. Smart molds can provide real-time data on performance and maintenance needs.
2. Sustainable Practices
As the global focus on sustainability heightens, manufacturers are exploring biodegradable materials and more efficient production techniques that reduce environmental impact.
3. Customization and 3D Printing Integration
Combining 3D printing with traditional injection molding allows for rapid prototyping and customization of complex designs, further enhancing the appeal of injection molding.
Conclusion
Understanding the intricacies of plastic injection molding empowers businesses to make informed decisions when considering investments in molds. By focusing on quality, efficiency, and strategic planning, companies can significantly enhance their manufacturing capabilities. Embracing best practices in selecting and maintaining molds can lead to lasting success in the competitive marketplace. If you are ready to elevate your production processes, take the first step and buy plastic injection molds that align with your business goals.